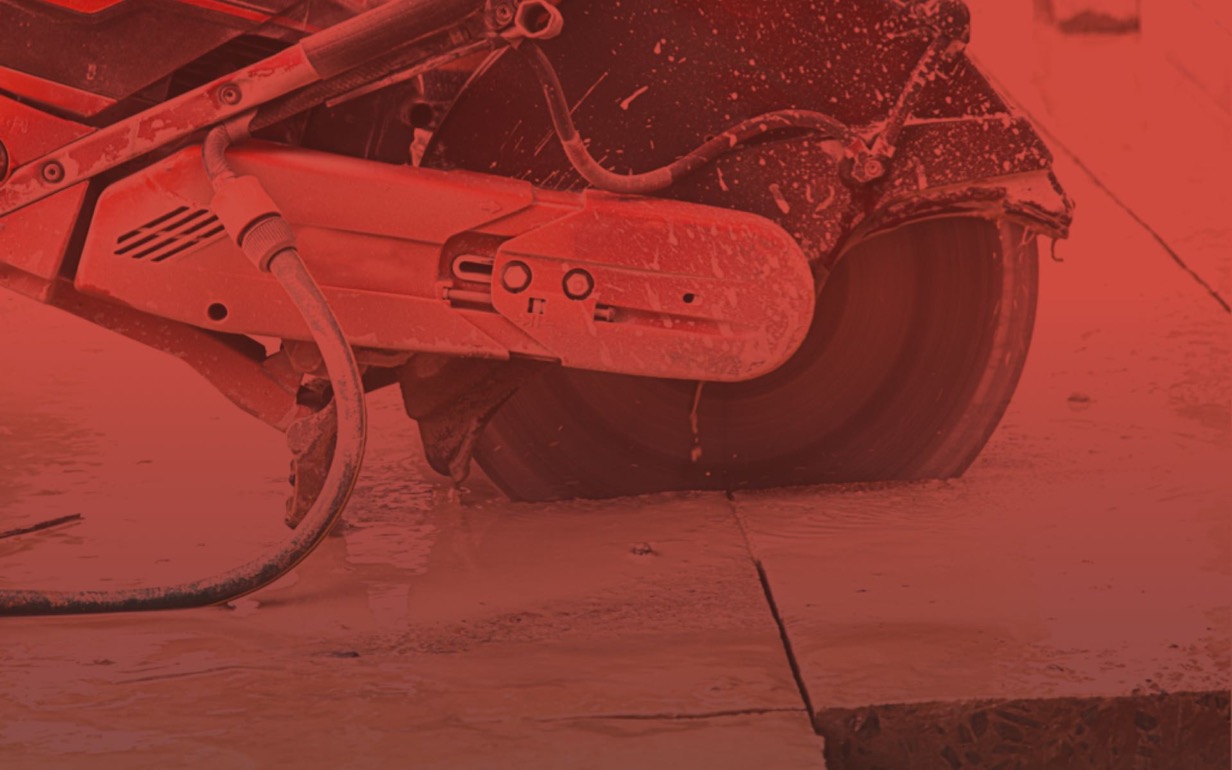
General Industry Silica
Crystalline Silica Hazards – You’re required unless you can prove that you aren’t
The most common OSHA citation is an inadequate or absent air monitoring program with the second most cited OSHA citations being an inadequate or absent exposure control plan. 39% of all OSHA citations fall under unsatisfactory respiratory conditions.
With such a large number of violations attributed to respiratory health it’s important to formulate a respiratory plan that fits your needs as an employer. The General Industry Silica standard guides employers on providing a safe working environment for employees who might encounter some of these obstacles on a daily basis. We’ve outlined some areas below to pay special attention to!
- [1910.1053(a)(2)], [1910.1053(d)(1)] – Employer Responsibilities
- [1910.1053(d)] – Exposure Monitoring
- [1910.1053(f)(1)] – Engineering and Work Practice Controls
- [1910.1053(f)(2)] – Written Exposure Control Plan
- [1910.1053(g)] – Personal Protective Equipment/ Respirator
- [1910.1053(j)] – Hazard Communication
- [1910.1053(j)(3)] – Employee Training
Does the General Industry Silica standard apply to me?
Quite possibly. Under OSHA’s General Duty Clause (Section 5(a)(1) of the OSH Act) employers are responsible for protecting their employees from a hazardous working environment.
Content Preview
General Industry Silica |
Revision: | 0 | |||
Date: | 8/31/2025 | ||||
Prepared by: | |||||
Approved by: |
1.0 INTRODUCTION
The Crystalline Silica Dust Program has been established by Acme Inc. to protect employees from occupational exposure to respirable crystalline silica. This program is designed to provide a safe and healthful workplace and to satisfy the requirements of the OSHA’s 29 CFR 1910.1053 Occupational Exposure to Respirable Crystalline Silica.
2.0 RESPONSIBILITIES
2.1 Program Manager
2.1.1 Overall administration of the Respirable Crystalline Silica Program. 2.1.2 Perform personal occupational exposure sampling. 2.1.3 Notify employees of their occupational exposure sampling results. 2.1.4 Recommend appropriate administrative controls and personal protective equipment (PPE). 2.1.5 Provide respirable crystalline silica training for employees. 2.1.6 Evaluate new equipment and process changes relative to the potential for occupational exposures. 2.1.7 Schedule and perform silica physicals and conduct retesting at least every three years or sooner if appropriate. A silica physical shall consist of the following:
- Work history
- Patient history
- Check for respiratory system dysfunction
- Chest X-Ray
Subscribe to the All-Access Membership or purchase this plan a la caret to access the full contents...
Ready to Start Your Safetly Plan?
Create a General Industry Silica plan for your organization in just a few show steps.